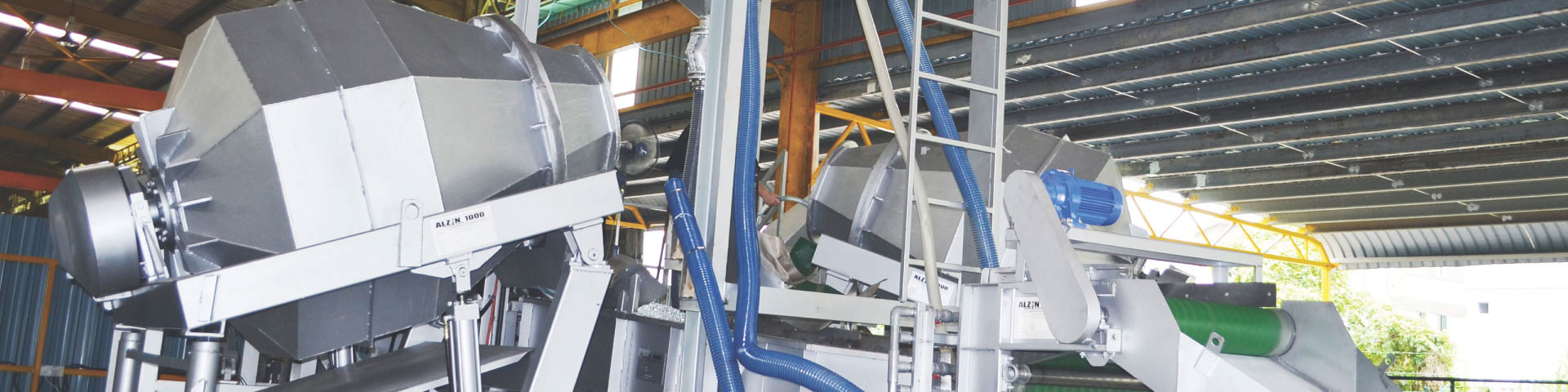
MECHANICAL ZINC
A PREMIUM CORROSION RESISTANT COATING FROM MENARA KERJAYA FASTENERS
Nowadays, surrounding environment condition and climate change have influenced the deterioration process of building materials. Corrosion is one of the common deterioration that caused by the deterioration of metal due to chemical reaction as a result of exposure to the environment. Air pollutions and climate factors have directly or indirectly decrease the service life of the building and its component’s performance such as steel roofing and fasteners. Exposure to corrosion can dramatically affects the performance of fasteners over their lifetime, subsequently affecting the long time structural integrity of any construction. Hence, corrosion protective coatings placed on fasteners must be able to withstand the corrosive action in order to achieve a reasonable service life. In fact, steel fasteners only form a very small portion of the total cost of any construction but incorrect selection of the fasteners with desired quality and corrosion protection could cost a fatal failure in structure integrity.
In line with our principal to provide high quality value added products to our customers, we had collaborated with ALZIN COATING SYSTEM, one of the industry leaders in developing a premium corrosion resistant coating known as Mechanical Zinc. Menara Kerjaya now owned a largest Mechanical Zinc Plating system in South East Asia which able to cater rising demand on corrosion protective fasteners. Our plating system has the ability to plate many varying standards such as Australia Standard AS3566.2 Class 2, Class 3 and Class 4 and ASTM 695. Our Class 2, 3 & 4 coatings have been designed to suit the harsh tropical climate and are comply 100% with the AS3566.2 and also applicable to ISO9223 environment category Class 2, 3 & 4.
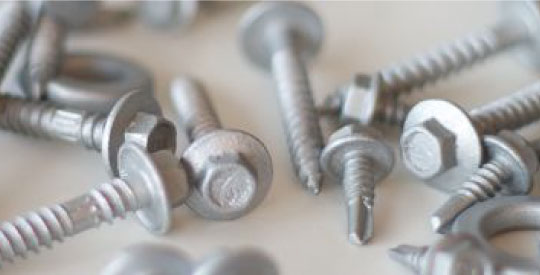
WHAT IS MECHANICAL ZINC?
Mechanical Zinc is an excellent coating method that imparts a superb metal surface finish on ferrous metal components for providing long-term corrosion protection. Mechanical Zinc process uses kinetic impact energy of “impact media”, along with special chemicals and zinc alloy powder to create an adherent, uniform, highly corrosion resistant finish in a wide range of coating thicknesses.
Mechanical Zinc engineered to combat the extreme effects of salt, wind, and moisture that found in marine and tropical environment.
CROSS SECTIONAL ANALYSIS AND SALT SPRAY TEST
Cross sectional analysis at 500x magnification to our Mechanical Zinc Class 3 fasteners, shows a very even coating at the required thickness as well as having a density rating of 9-10.
Chemical analysis of the coating also showed 79% Zinc and 21% Tin which fulfilled the requirement of AS3566.2 Table 2.
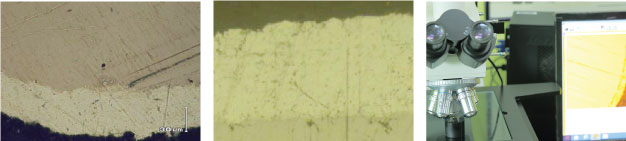
Our Class 3 & Class 4 plated fasteners also tested in ASTM B117-03 Salt Spray Test. The salt spray test result indicates that there is no significant sign of Red rust at 1,000 hours.
This is due to the nature of the sealers rather than the base metal protection. Please note that Salt Spray Test bears no reflection to real world performance.
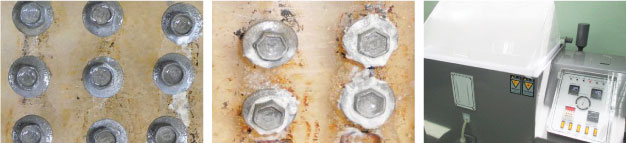
WHY USE MECHANICAL ZINC PLATED FASTENERS?
Superior Corrosion
Resistance
Superior performance against salt water, UV, weathering and others.
Free From Hydrogen
Embrittlement
Pickling and electrolytic processes are not necessary for our process make it ideal for High Tensile parts.
Corrosion Resistance
Against Scratches
Minimal surface scratched due to solid composite layers.
Low Processing
Temperature
The process is at room temperature that does not de-temper the heat-treated parts.
Excellent Adhesion
Because of the underlying coatings, Mechanical Plating has excellent adhesion to the base metal.
No Galling Issue
Because of the composite nature of mechanical coatings, this naturally lubricious coating will not gall, producing more accurate torque-tension relationships.
REAL WORLD OUTDOOR EXPOSURE TEST
Developed in Australia by ALZIN COATING SYSTEM, our Mechanical Zinc Class 3 & 4 coatings are specifically designed for ISO Category Class 3 & 4. These coatings have been evaluated and tested on an outdoor exposure test site which is situated on one of Australia’s most corrosive southern island. Outdoor test site expose the fasteners to the combination of corrosive influences that exist in the real world including salt spray, humidity, ultra-violet light, acid rain and compatibility with roof sheeting. The result from the real world test is then replicate in a lab environment to ensure the life prediction is accurate. Our coatings have been developed and improved as a direct result from what has been learned during the testing.
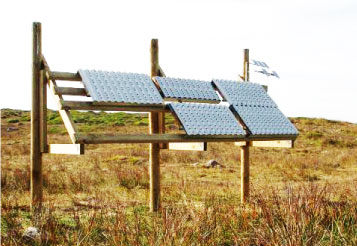
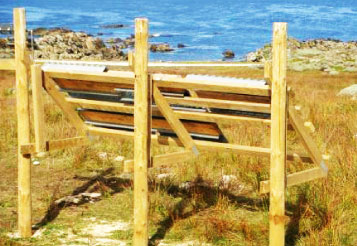
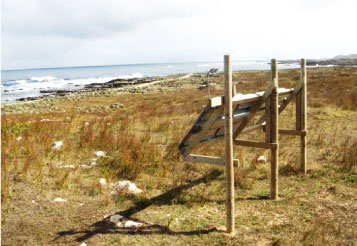
Corrosion Resistance Requirement in accordance to Australia Standard AS 3566.2-2002 Table 2
The Australian Standard for fastener performance (AS3566) was introduced in 1988, amended in 1990 and ratified in 2002. The requirement and classes of corrosion resistance for Mechanical Zinc Plated are listed as below:
Corrosion Resistance Class | Coating Composition | Min. Local Metalic Coating Thickness | Minimum Porosity Rating of Coating |
---|---|---|---|
2 | 20-30% Tin Balance Zinc | 12 | 6 |
3 | 20-30% Tin Balance Zinc | 25 | 8 |
4 | 25-30% Tin Balance Zinc | 45 | 8 |